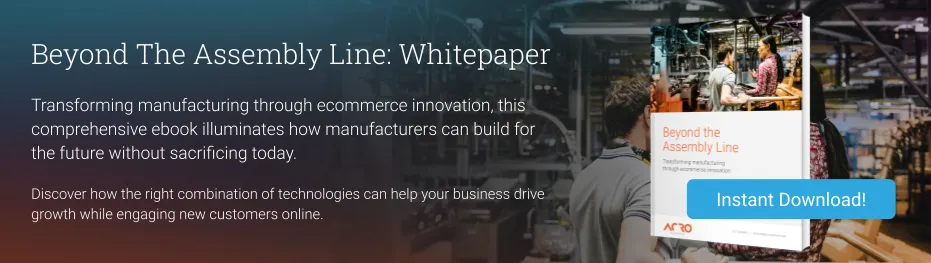
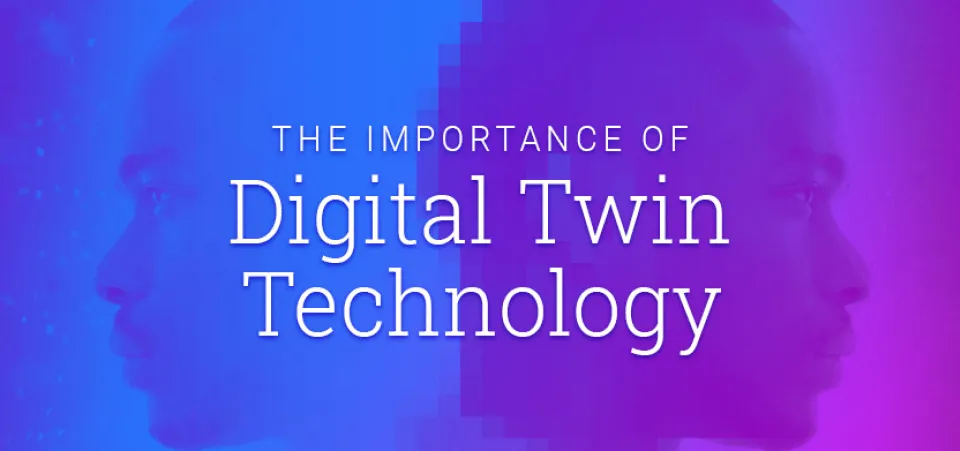
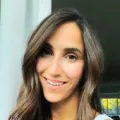
Posted in Automation
May 25, 2021
The importance of digital twin technology
A digital twin is a virtual copy of a physical object, system, or process. This digital version allows data scientists to use them to run simulations before physical versions are built and deployed. Nowadays, some of the largest companies are using digital twins, changing how artificial intelligence and analytics are optimized. Digital twins can also be used to analyze copies of existing physical assets and find ways to optimize them or use the data that sensors collect to anticipate future needs of those physical assets, eliminating downtime due to failure.
Digital twins have expanded to include large items such as buildings, factories, cities, and even people and processes. In essence, a digital twin can be described as a computer program that contains real-world data about an object or system, showing predictive outputs based on inputted data.
How are digital twins used?
Digital twins are constructed to simulate an object or process in real-time, offering performance insights and potential problems. The twin could also serve as a prototype before the physical product is built, providing feedback for product refinement. For example, digital twins are also used for maintenance operations to test a proposed “fix” to a piece of equipment before applying the fix to the physical equipment.
“Digital twins offer strong potential to achieve better insights on their objects and drive better decisions.” - Gartner, How to Use Digital Twins in Your IoT Strategy.
Business sectors such as automotive, healthcare, food & beverage and manufacturing have all implemented digital twin technology. In the case of manufacturing, where the technology is arguably the furthest along, factories use digital twins to simulate their assembly process.
- Deloitte reports a scenario where an industrial manufacturer reduced rework by 15-20% through improvements to their assembly process from the insight gleaned from the digital twin analytics data.
- Chevron is also in the process of using digital twins for its oil fields and refineries and expects to save millions of dollars in maintenance costs.
- General Electric Co, an early adopter, now has over 1.2 million digital twins of physical assets.
“For every physical asset in the world, we have a virtual copy running in the cloud that gets richer with every second of operational data,” says Ganesh Bell, chief digital officer and general manager of Software & Analytics at GE Power & Water.”
The expectation is that digital twins will continue to become more widespread, creating virtual facility models and giving managers a more complete view of their operations. This includes highlighting what’s working productively and what’s causing downtime and lost profits.
In summary, digital twins are exciting, fast-growing and advantageous, not just from a maintenance perspective but also in profitability. However, according to Gartner, it’s also important to remember that digital twins aren’t always called for, as they can create unnecessary complexity and concerns for privacy and integration.
Digital twins may not be right for every instance of manufacturing and industry, but they do provide an amazing amount of insight and data for those enterprises that have implemented them. One of the main benefits of digital twins is identifying areas in which workflow automation can benefit an organization.
If automation is on your manufacturing business’s to-do list, talk with an Acro Commerce subject matter expert today.
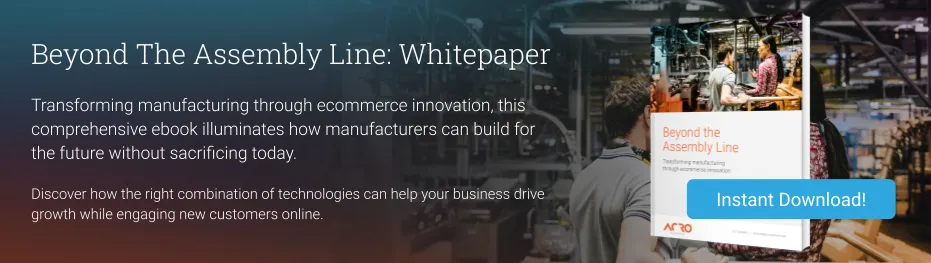